CNH Industrial inaugurated its agricultural dynamic simulator in Modena, Italy. The simulator verifies the dynamic behavior of a tractor before it enters production. The San Matteo R&D Center is home to CNH’s first agricultural-sector application of this technology.
Designed and built by a team of engineers based in San Matteo, the Dynamic Simulator is the culmination of a year-long project and represents a significant investment in both technology and innovation. This is in addition to the creation of 150 new jobs since the start of the year, 120 of them for engineers recruited to work on the R&D Center’s core areas of focus. They are accompanied by new graduates, for whom CNH Industrial offers excellent career prospects – thanks also to its partnerships with leading technical universities in Italy and Europe.
“The San Matteo R&D Center is a state-of-the-art facility for the engineering and technological development of our tractors globally,” said Carlo Alberto Sisto, President EMEA, CNH Industrial. “CNH Industrial’s investments have further reinforced research, both in the more traditional areas of mechanical and electrical engineering, and in electrification. And will see San Matteo become the Company’s main European electrification hub.”
In August, the Italian Ministry of Economic Development signed an innovation agreement which saw the site awarded €39.4 million, of which €7.9 million was assigned to the development of hybrid-electric technology for tractors. This further confirms the R&D Center’s significant contribution to the future of electrification.
The virtual simulator is included within the overall framework of this investment, as it facilitates performance enhancements using sustainable technology – as foreseen by the company’s strategic plan.
In practical terms, the dynamic simulator verifies the dynamic behavior of the equipment – a tractor in this initial version – before it enters production. It can predict potential issues, and resolve them before they occur, even before the machine enters service.
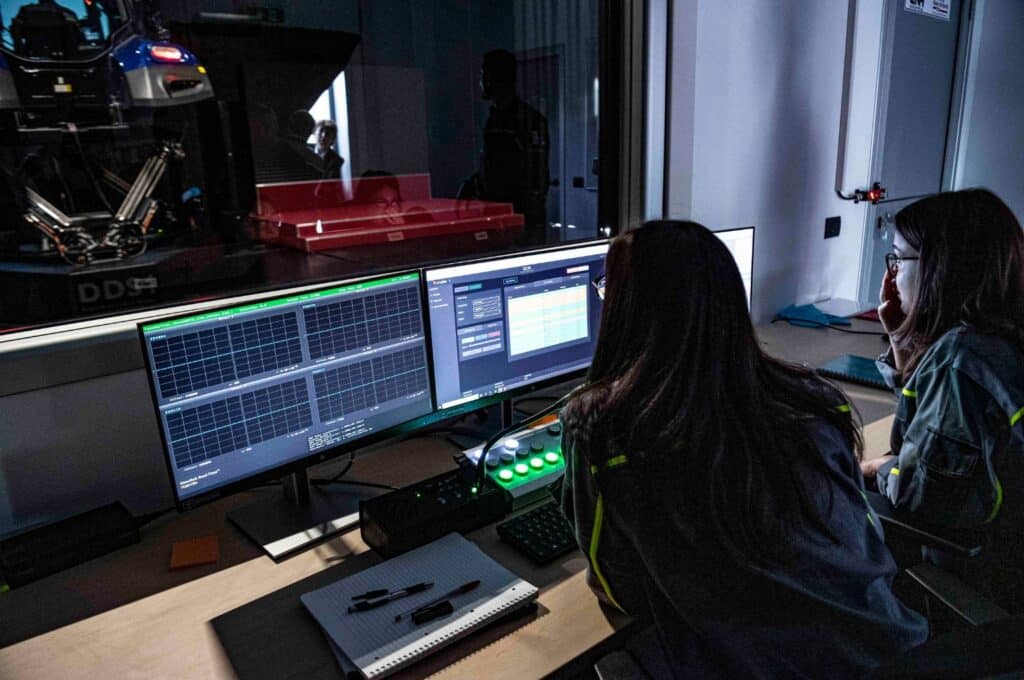
“The dynamic simulator forms part of CNH Industrial’s virtual testing activity. It marks a revolution in our industry, where technology can really make the difference in the development of ever more sustainable, advanced and safe products,” said Carlo Lambro, brand president, New Holland Agriculture and CEO, CNH Industrial Italia.
There are real world benefits for CNH, customers and the local community including lower development costs, faster time to market and products which feature the latest technology – increasingly focused on lowering carbon emissions to improve the sustainability of the entire industry. What’s more the simulation enables “man-in-the-loop” design – designers can interact with the various controls and discover how the equipment responds right from the beginning of the design process.
The dynamic simulator completes the core set of skills and tools developed by the CNH Industrial virtual simulation team. Over the last 10 years they have produced an integrated virtual simulation environment which can test the core functions of the Company’s entire product line up – in effect producing ‘digital twins.’ To support this strategy CNH Industrial has increased its HPC (High Performance Computing) infrastructure five-fold just this year.