The new Jumbo 7000 flagship loader wagon has been designed for maximum performance and the greatest efficiency. All the core components have been completely redesigned and engineered for tractors outputting up to 500 hp. It comes with numerous patented technical innovations that make harvesting more efficient. The third generation of this high-performance series has also been given an appealing facelift. The most important new features at a glance.
To keep the forage clean, the 7-row controlled floating pick-up with a working width of 2,300 mm ensures maximum performance for tidy and loss-free collection in a single pass. The pick-up’s new hydraulically adjustable drive system adapts the speed automatically to the driving speed. There is less of a dragging effect and the result is perfect chopping quality. The jockey wheel steering system can be engaged to enable even better ground tracking.
The pick-up position control, which is supplied as standard, keeps the cross-section of the opening between pick-up and drawbar constant to ensure maximum throughput during the entire loading process. The tines, which are controlled in a sweeping arc by the cam track, convey the crop gently upwards and actively transfer it to the rotor at a suitable speed. Instead of dragging the forage through, they promote the best possible chopping quality. The tines then dip down at a right angle to prevent the forage from being drawn in.
To help the driver when accessing narrow field entrances, the optional hydraulic jockey wheel folding system can be activated.
The optional tracking roller prevents the pick-up wheels from sinking into tractor wheel marks and enables unrestricted movement for the best ground tracking. The wide additional tracking roller and the two jockey wheels form a stable support triangle for perfect ground tracking and, as a result, the lowest possible crude ash ingress.
The best forage for more yield
High yield dairy cattle need a high quality basic ration with optimum forage structure. Thanks to the POWERCUT short-length chopping system with an asymmetric array of 48 knives and a theoretical chopped length of 34 mm, you get to harvest the best quality forage. The long arc of the knives delivers a slicing cut along the full length of the blade. The forage is chopped right through exactly and uniformly. This makes the chopped material an ideally structured ruminant stimulating forage. The knife bank release system – handled without the need for tools – and the central knife release system are operated conveniently using a control panel to the side. Pure convenience.
Power transfer reinvented
The multi-purpose rotor loader wagon combines essential performance features for forage harvesting with those required for transport: highest throughput, clean crop intake, precise chopping quality, and high operational reliability for a loader wagon, and the flexibility and volume of a transport wagon. The new models have been engineered for tractors between 200 and 500 hp. This makes it the first loader wagon to reach the magical power limit of 500 hp, placing it well within the throughput capacity of a forage harvester.
Great attention has been paid to implementing a modern and innovative driveline concept: The driveline has a double wide-angle PTO shaft without a clutch and is powered by a Powerband. Optimum power transmission to the rotor is ensured by angular/planetary gears in the rotor drive. The Powerband delivers maximum power transfer in all operating conditions. It ensures smooth running and a damping effect in changing operating conditions. This protects the driveline and reduces maintenance and wear costs to a minimum.
The loading rotor
75 percent of the rotor’s width is fitted with a new high-strength case-hardened steel that ensures high wear resistance in areas subjected to a lot of wear. This increases service life by 25 percent.
With the new unloading beater driveline that delivers 210 kW, unloading capacity has been increased by another third: Unloading takes about 1 minute. The beater drive switch integrated into the angular gearbox is activated by the belt tensioner to ensure friction-locked start-up. The soft start protects not just the beater driveline elements but also the scraper floor drive and the chains. No power peaks occur and the service life is prolonged. The innovative shape of beater rotor with a V-twist conveys the crop uniformly and with no power peaks. They reliably loosen even highly compacted forage. The uniform blanket of forage output by the JUMBO facilitates the rollers’ work to guarantee efficient compaction and the best silage quality.
The moveable front panel provides a significant increase in volume of 4.3 m3 for the same length of wagon. This also makes the loader wagon much more compact. It is now more manoeuvrable in small fields and on narrow field tracks.
The patented, intelligent front panel enables a unique loading and unloading strategy. Available as an option, its length of 830 mm means it has a particularly generously dimensioned upper forage compression flap. An additional dynamometer bolt is fitted in the intelligent front panel to enable a new control concept. The loading pressure is now measured at the front panel. With the combination of all measuring points (loading torque sensor, dynamometer bolt, compression flap sensor), the degree of compaction and the desired filling level can be directly regulated. As a result, the parameters can be perfectly adjusted to the forage harvesting requirements. With the active forage compression flap, unique loading rates of up to 400 kg/m³ can be achieved if required, depending on the DM content.
Intelligent automatic loading system
Three predefined modes can be selected for loading, ranging from light loading to medium compression to high compaction. They enable optimum adaptation to different types of crop, the dry matter content and the degree of filling.
Depending on the job in hand and the requirements, the three modes can be selected for the most suitable filling strategy. The driver can program the set-up with predefined parameters and so vastly improve the overall cost effectiveness of the tractor and wagon combination. If the scraper floor is actuated by the automatic loading system, the front panel helps push the forage along and then automatically moves back into the loading position. This ensures that the forage stays extremely compact.
In addition, two 2-speed motors – mounted externally on both sides – and a patented boost function, ensure maximum unloading performance. To give the driver a clear view from the tractor into the loading chamber or for driving in under the harvester auger in harvest transport mode, the compression flap can be hydraulically folded forwards.
The scraper floor has been lowered at the front by 250 mm to reduce the power required during loading. This also increases the net payload thanks to higher compaction. The wide flat link chains with a breaking load of 13 t provide great stability, maximum reliability and smooth running.
The scraper floor slats are double-bolted and rest on exchangeable guide bars. Thanks to its high power transmission and compact construction, the JUMBO is suitable for transporting all kinds of chopped material.
Another advantage when using the wagon in transport mode is that the pick-up can be removed. This reduces the weight of the JUMBO by 520 kg and protects the pick-up from damage. The pick-up can be removed using an optional handling trolley.
As a multi-purpose loader wagon, the JUMBO is also a fully-fledged transport wagon that can be used for transporting materials other than grassland harvest. By removing the pick-up, transport capacity is quickly and easily increased. The newly designed loading chamber cover retains the load and secures it ready for transport on the road.
Making reliability a priority
The hydro-pneumatic tandem and tridem chassis provide a wide support spacing of 1,100 mm and 856 mm at the steered axles for safe handling, exceptional stability on steep ground as well as enhanced safety when driving at high speeds. The unique mechanical anti-roll bar effect is achieved by integration of longitudinal linkage springs on the chassis, the bolted connection of the axles and the wide spring spacing.
The large axle compensation of up to 270 mm ensures better climbing ability on inclines, in the clamp and on poor quality roads. The hydro-pneumatic axle compensation ensures uniform wheel pressure in all operating situations. An impressive increase in driving comfort has been achieved by fine-tuning the suspension characteristics. Using a different hydraulic accumulator when the loader wagon is empty from the one when the wagon is full noticeably increases driving comfort.
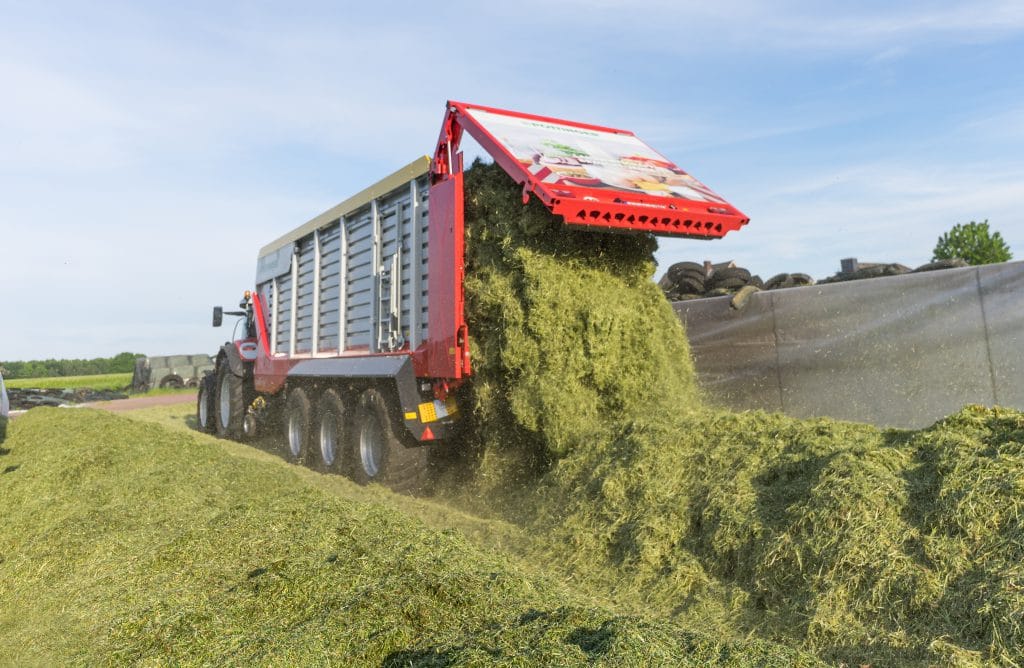
Safe and sound
The newly designed load retention system covers the load and secures it ready for transport on the road. The cover consists of two folding frame sections with a hydraulic chain drive mounted at the centre of the shaft.
The “Easy move” swing-out knife bank makes it easy to change and reverse the knives. The knives are made of hardened “Durastar” tool quality steel for a 20 percent longer service life. A patented individual knife protection system protects the loader wagon and subsequently the livestock.
Turning instead of changing, is the way to go with the “Twin Blade” reversible knife. Its patented shape ensures double the service life. No need to sharpen or carry a second set of knives: please turn over!
The patented individual knife protection system protects the loader wagon and the livestock. The triggering pressure of the knife protection system has of course been adapted to the high throughput capacity. At the same time, the knives are held in the correct position to make sure that they chop consistently.
The “Autocut” knife sharpening system enables the knives to be sharpened full automatically directly on the loader wagon. Permanently sharp blades can reduce fuel consumption by up to 15 percent. Another positive effect is that maintenance work is reduced by up to 45 minutes per day. The sharpening process can be carried out conveniently during a break. Thanks to the new electric-hydraulic drive system, the sharpening time is now even shorter.
Intelligent control
Pöttinger’s answer is the “Power Control system” and the Expert 75 and CCI 1200 Isobus terminals. These terminals replace the numerous implement-specific units on-board and enable professional operation of all Isobus-compatible machines, regardless of whether they were made by Pöttinger or other manufacturers.
Harvesting with the loader wagon process guarantees the best quality forage and silage at low harvesting costs, More than ever before, the new Jumbo is all about optimizing the harvesting process, from efficient collection in the field to the best quality ration.